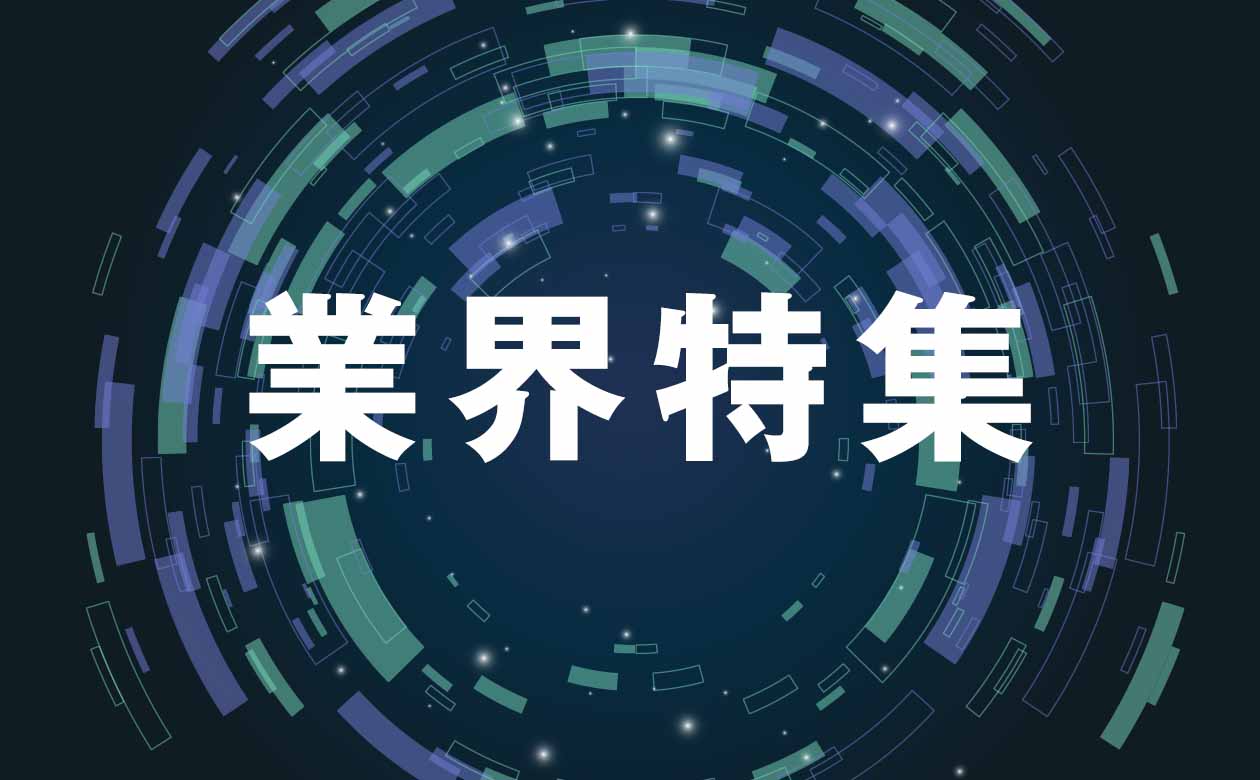
業界特集
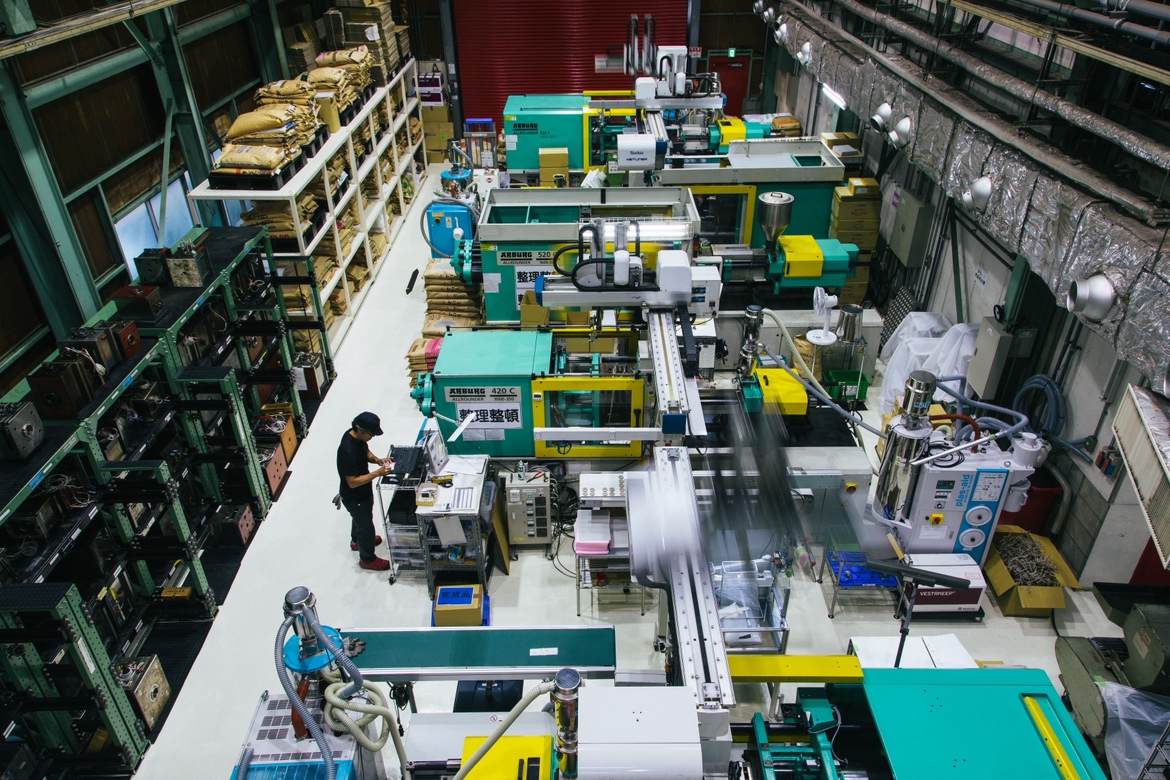
株式会社ダイプラ
掲載企業株式会社ダイプラ
-
主要3品目
-
スーパーエンプラ成形
インサート成形
PEEK
PEEKの射出成形実績は日本トップクラス
PEEK(ポリエーテルエーテルケトン)を始めとするスーパーエンジニアリングプラスチック成形で困ったときには声が掛かる。樹脂メーカーから厚い信頼を得ている成形工場がある。それが大阪市にある株式会社ダイプラだ。PEEKを取り扱って40年。現在では、売り上げの80%をエンジニアリングプラスチックとスーパーエンジニアリングプラスチック成形が占める。PEEKの射出成形実績ならば日本トップクラスという自負がある。
きっかけは、一台のドイツ製射出成形機だった。同社はスピーカー部品など、インサート成形を得意とする成形工場だった。競合が多く価格競争に巻き込まれることを懸念していたなか、出会ったのがArburg(アーブルグ)社製ユニバーサルモデルだ。これは竪型にも横型にもなる画期的な射出成形機で「これこそダイプラのために作られた成形機だ」と感動した代表取締役会長の大東章男氏は、すぐに導入を決めた。
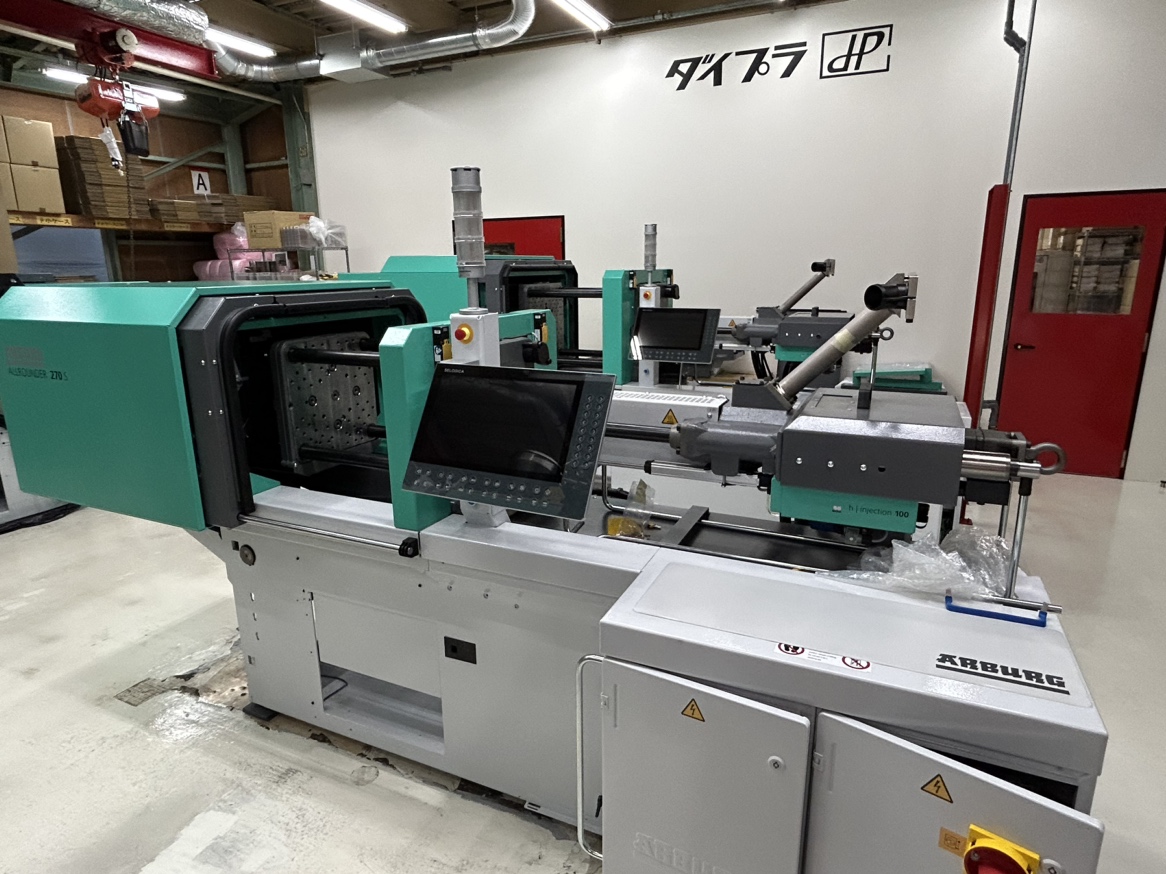
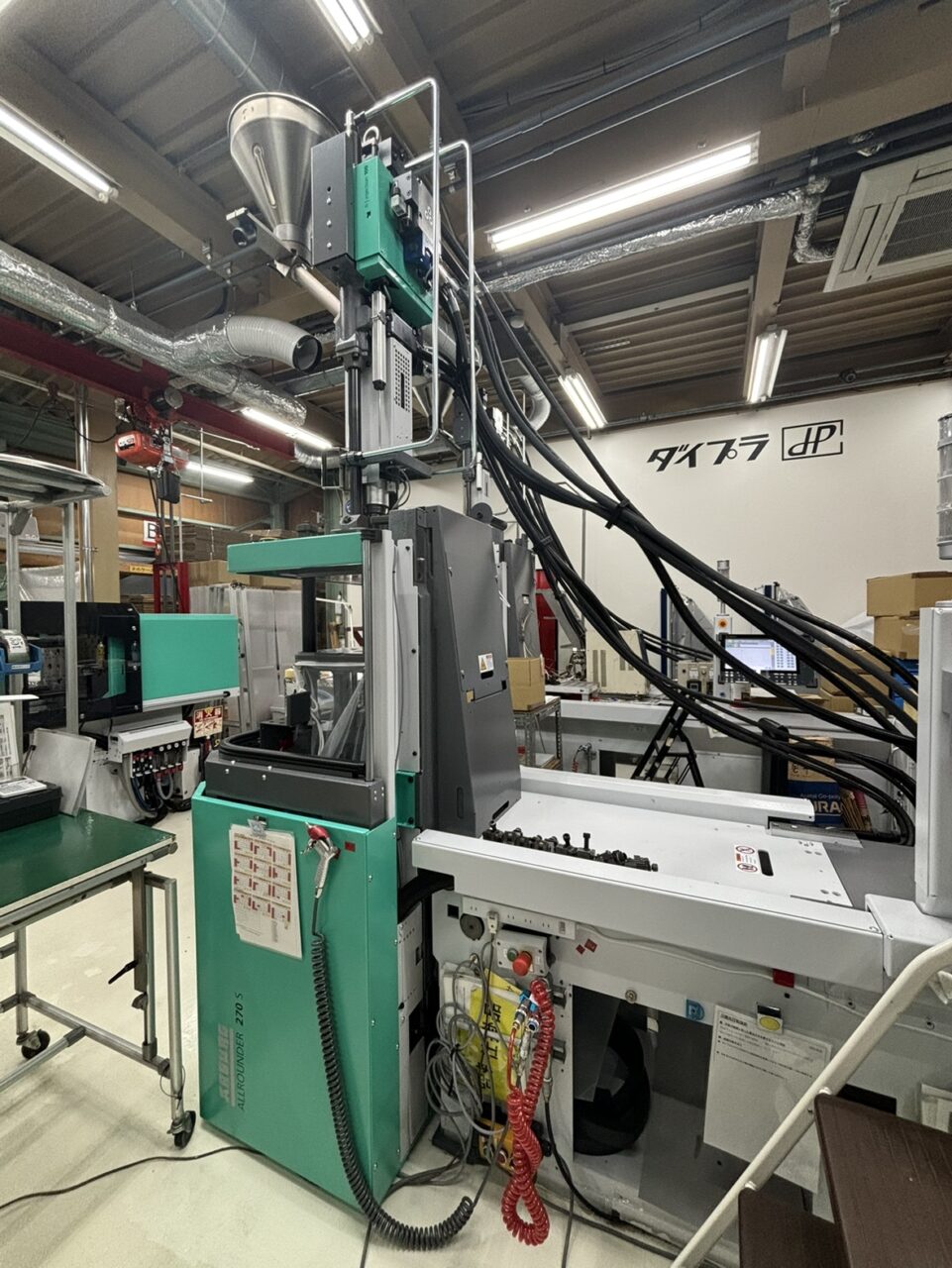
このドイツ製高性能射出成形機を導入したことで大手チェーンメーカーからPEEKの成形を持ちかけられたのが、同社とスーパーエンジニアリングプラスチックの出会いだ。同社では無給油チェーンローラーの肉薄スリーブの試作に成功。チェーンメーカーも驚き、以後開発案件が舞い込むようになる。
PEEKは、耐摩耗性、耐熱劣化性、耐薬品性など優れた特性を持つ。どんな金属材料でも適合しなかった部品が、PEEKならばできたという話もあるほど。ニッチでもPEEKにしかできない分野が確実に存在する非常に魅力的な材料でありながら、まだまだ知られていないのが現状だ。同社でも導入以降、ニーズとマッチしなかった時期が長く続いたと言うが、液晶や半導体の製造設備、医療用途などで導入が進んでいるだけでなく、バネ形状の成形品など、新しい分野にも挑戦を続けている。今後も更なる需要拡大が期待されているのだ。
高負荷価値を生み出す技術力
アーブルグ社製射出成形機と共に導入されたドイツ式経営理念
PEEKは優れた特性を持つ一方で、流れにくく、成形温度は380~450℃、金型温度は180~250℃。さらに成形時にはガスが多く発生するため、ガスベントなどのノウハウが必要となる。同社がPEEKを導入当時、まだ日本ではスーパーエンジニアリングプラスチックは知られておらず、成形技術も発達していなかった。大東氏は独学で成形技術を勉強し、経験を重ねノウハウを蓄積したのだ。そのノウハウは現在、3D設計技術とともにアップデートされ継承されている。
同社ではこのノウハウを生かし、成形だけでなく設計支援も合わせて行っている。客先からのポンチ絵レベルを基に、精度の高い3Dデータでの設計支援、光造形のモデル製作までを無償で行っているのだ。品質管理や問題が起こったときの対応の早さにも自信を持っている。スーパーエンジニアリングプラスチックは汎用プラスチックに比べ、材料代だけでも何十倍、何百倍もの価格差がある。その上同社の加工費は高付加価値製品が多いため、より高く設定されているが、それでも顧客が途切れないのは、同社の技術力だけでなくこうした手厚いサポート体制が評価されているためだ。
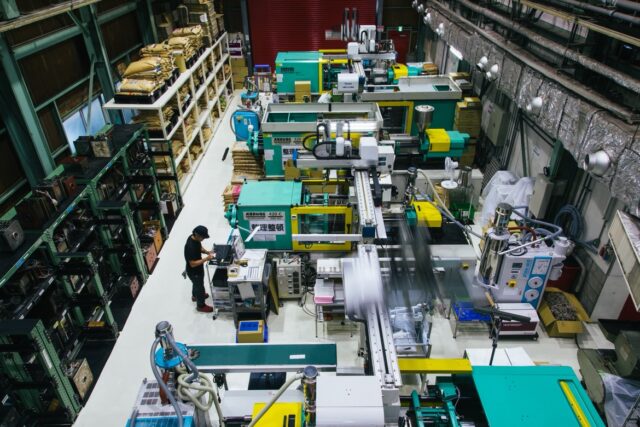
ダイプラでは4年前に全ての射出成形機をArburg社製へ入れ替えた。大東氏がドイツに感銘を受けたのは、機械だけでなくその経営理念にある。賃金の低さや厳しい労働環境と言った日本の製造業を取り巻く問題に、大東氏はこう答える。「本当の生産性を上げるというのは、短い時間で多くの成果を上げること。そのためには経営者が強い意志を持って技術的な改革をしなくてはなりません。当社ではPEEKに限らず、PS(ポリスチレン)からCOP(シンクロオレフィンポリマー)への代替、PBI(ポリベンゾイミダゾール)のような非常に成形が困難な材料にも実績があります。スーパーエンプラでお困りの方はぜひ声をかけてほしい」と大東氏。他社ではまねのできない技術力を強みに、ダイプラでしかできない製品作りとサービスを提供し続けている。
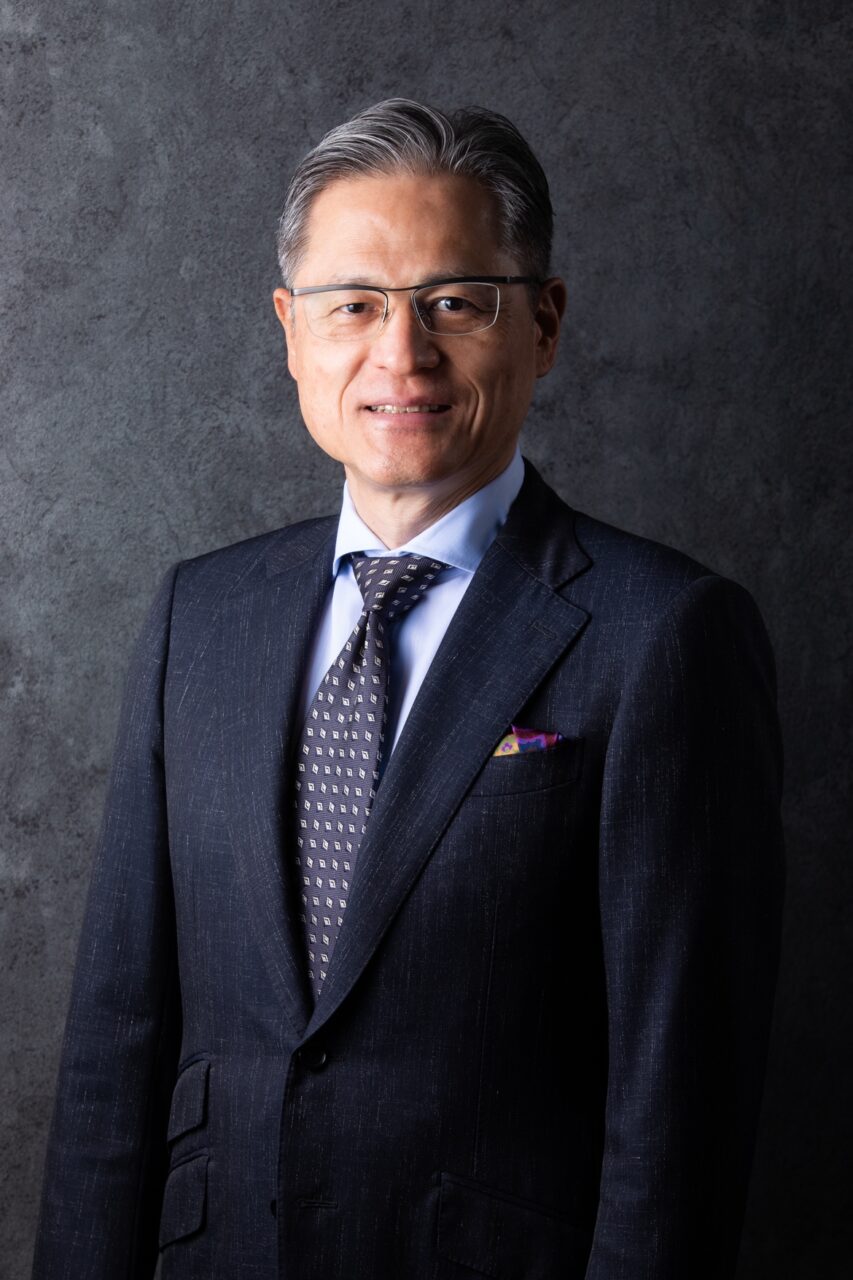
大東 章男氏
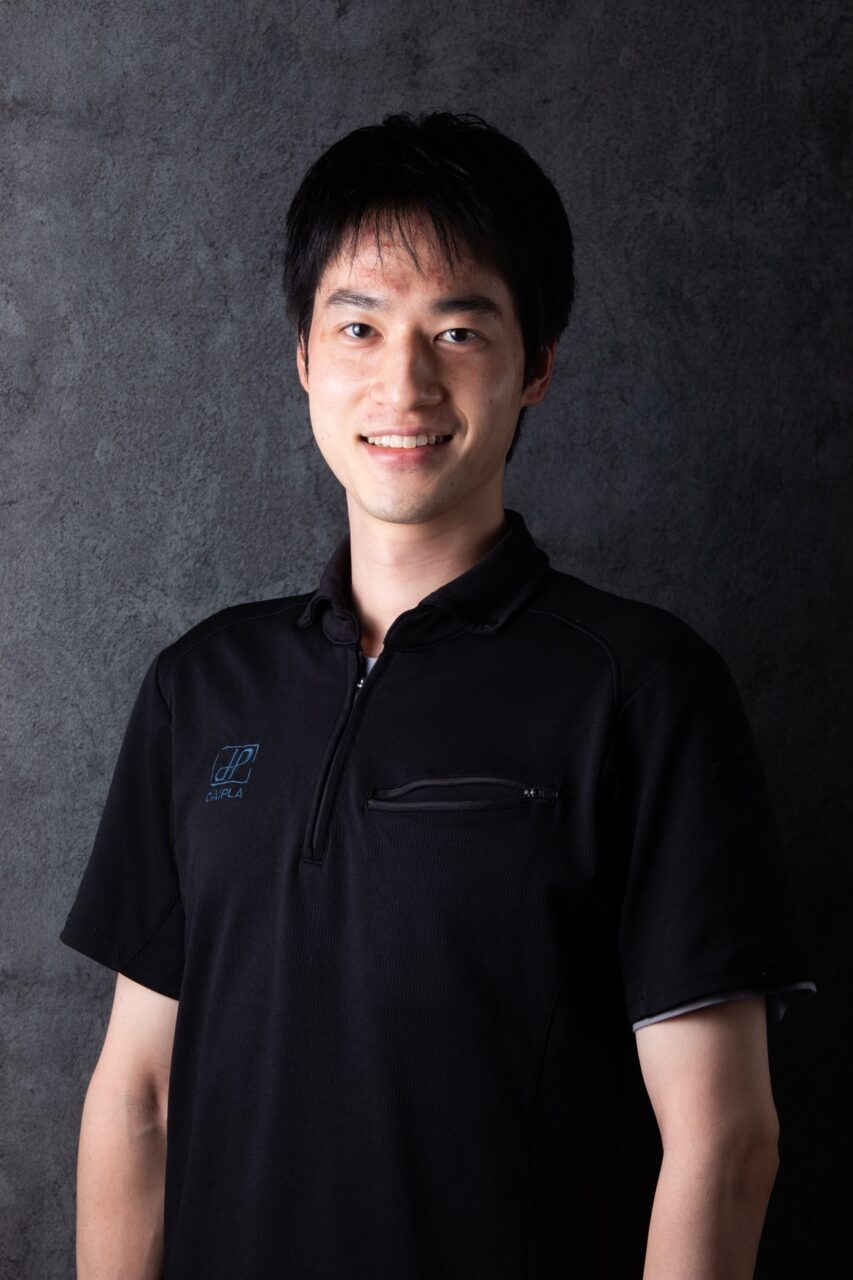
大東 恵太氏